About Granger Industries Inc.,
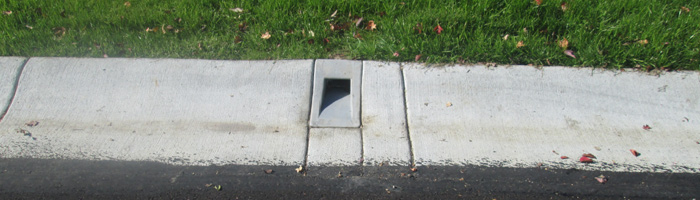
Granger Plastics Company, initially founded in 1994 by John Grimes, a 40 year pioneer to the Rotomolding market. His father, John Grimes Sr., was one of the original inventors for materials to the Rotational Molding industry. Inside of 2 years of Granger Plastics startup, it swiftly outgrew its initial Sharonville, OH facility. In 1996, needing a bigger production center and more warehousing space, Granger Plastics soon transferred to Middletown, OH another Metro Cincinnati-Dayton location suburban area.
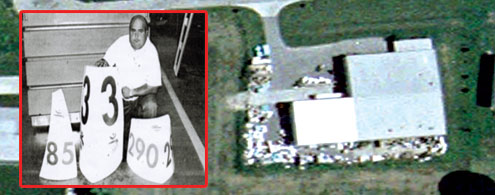
Through continued development of Granger Plastics, the plastics business had actually begun to out grow its fairly new address. In 1998, it was identified that Granger Plastics would be forced to make big capital expenditures, broadening its company and capabilities at its new address. The additonal abilities, equipment and extra client base would need including another principal to the business. The partner was an extremely pursued, partner of Mr. Grimes past in Rotational Molding. The brand-new partner, Jim Cravens, would be generated at a crucial point in Granger Plastics already short history. It was a memorable period of change at Granger Plastics Company, as opportunities originated from brand-new directions.
Prior to 2000, Granger Plastics Company had actually already begun understanding that it would need to expand once again to its recently acquired Middletown, OH place. Granger Plastics was shipping parts all over the world and would help to innovate a large range of markets, with fresh originalities and innovations. In 2002, John Grimes, after nearly 50 years of effort and devotion to the Rotational Molding industry and bringing Granger Plastics Company to a level of international promenience, John Grimes would choose to retire. This would leave Granger Plastics Company under the direction and guidance of Jim Cravens.
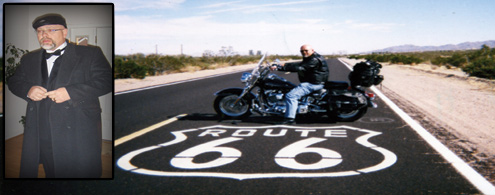
Plastics Molding Diversity
aerospace, defense, safety, material handling and much more!
Granger Plastics Company, has gained international promenince as a custom Rotational Molding Company, producing a large number of custom plastics solutions for a wide variety of international industry leaders. These companies display a wide variety of industry leaders in a multitude of industries ranging from Aerospace and Commercial Airlines, Defense and Safety, Chemical Manufacturing, Intermediate Bulk Containers, Material Handling, Memorial Products and so much more. Granger Plastics Company also performs a number of material conversions for OEMS and companies who look to improve their products by converting them from metals, fiberglass or other materials to plastic materials such as polyethylene and polypropylene. is an internationally recognized leader in Rotational Molding. Rotational Molding, or Rotomolding, is a plastics molding process that is produces large, durable hollow products, that have some of the most durable physical properties of any man made materials.
![]() |
![]() |
Conversions to plastics
Lower maintenance costs, increased durability!
Granger Plastics Company has worked with a number of industry leaders to convert existing products or components of products into plastic materials. Numerous of these conversions have came from OEMS who are experience an increase in their products quality and durability by converting from either metal based materials such as stainless steel or aluminum. Granger Plastics Company also commonly converts products and components from Thermoset materials, such as Fiberglass, Polyesters and more.
Granger Plastics Company has recently garnered international media attention after converting an extremely large fiberglass product to a much more durable, rotationally molded plastic product. The conversion from a fiberglass product to a plastic product has offered a tremendous increase in maintenance savings for one of the world's leaders in luxury automobile transportation.
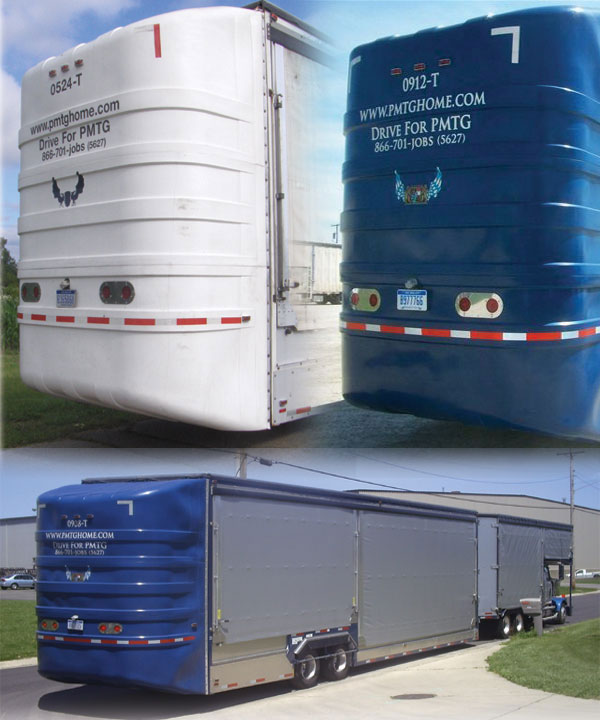
"Having introduced the world's first all-polyethylene rear trailer 'cone' as the replacement for 'cones' that have historically been fiberglass, we are pleased to advise that the new PolyCone produced by Granger Plastics Company is performing well in the field: Better impact resistance, better scuff resistance and lower cost. When a PolyCone is dented in the field, we just push it back into its original shape and send our enclosed car hauling equipment back on the road. Damage to fiberglass has always required bodywork to repair. We are pleased with the results of our material conversion project with GPC."
- Jim Prang
- Director of Maintenance
- Precision Motor Transport Group
- Okemos, MI